.png)

WHAT WE DO
WHAT WE DO
The Kolat Brick Company manufactures low cost, high strength construction products and provides best practice guidance for the utilisation of our products in a wide range of construction projects.
Our primary product is a hydraulically compressed interlocking clay brick, designed and manufactured for the private and public sectors in Sierra Leone.
The company has a social impact mission to develop and grow the business in order to provide full time employment in the remote community of Rogbere, stimulating and sustaining the local economy.
Kolat adopts the Hydraform Alternative Building Technology System using local clay soil to produce hydraulically compressed, interlocking bricks. This low-tech, cost-effective construction method is a proven system across the developing world.

THE KOLAT SYSTEM
This system has been proven and developed over 30 years across Africa and beyond by Hydraform. Using locally sourced materials we manufacture strong, high quality interlocking bricks that are dry stacked to build a wide range of projects including all styles of housing through to commercial and industrial units, hospitals and schools, including multi-storey buildings.






Excavate clay soil locally
Sieve and prepare clay soil
Dry mix sieved clay, sand and cement
Load mix into mechanical hopper for mixing with water
Hydraulically compact mixture to form brick
Leave under cover to cure for 21 days watering regularly
KOLAT MACHINES
Our 2 existing machines, the original Hydraform M7M1 and the M7M1 SUPER have recently been completely refurbished using authentic parts from Hydraform in South Africa.
​
In addition, we have recently taken delivery of a brand new Hydraform M7M3 with a double hydraulic chamber, 300 litre pan mixer, mechanical soil pulveriser and rotary sieve, which will allow increased production output.
​
Please see below and follow the links for further information.

Hydraform
M7M1 Original
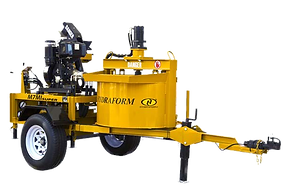
Hydraform
M7M1 Super

Hydraform
M7M3 Static
PRODUCTS
Our main product is the standard 180mm conduit brick.
We can produce 220mm and 150mm standard bricks for special order with minimum quantities of 1500 per size.
HYDRAFORM SYSTEM
The Hydraform Interlocking Soil Brick (hydraform brick) is an interlocking earth brick used in many countries for construction purposes. The hydraform brick is made from soil cement which is a mixture of soil, cement and water, and is hydraulically compressed to form a high quality interlocking soil brick. Soil from the building site can be used to manufacture building bricks.
​
The Hydraform compressed earth brick is very popular due to the cost savings that are involved during the construction process as only around 30% of the structure requires mortar between the bricks. Due to the interlocking nature of the stabilized soil brick, unskilled labour can be utilised in construction thereby empowering rural communities and creating jobs.
​
The bricks interlock top to bottom and front to back. Brick dimensions are 180 millimetres (8.7 in) wide, 115 millimetres (4.5 in) high and 230 millimetres (9.1 in) long. They weigh approximately 10 kilograms (22lb). Once bricks are manufactured they are "wet cured" for a period of 14–21 days to reach the desired crushing strength of 7Mpa or 7N/mm2.
HYDRAFORM HISTORY
Hydraform, like all great companies, started business based out of Jochen Kofahl’s garage, back in 1988. Jochen had a dream that high-quality bricks could be created with nothing more than a 20-percent addition of building cement to soil, formed in a machine under hydraulic pressure. That dream gave rise to South Africa’s first brickmaking company that designed, developed and marketed a patented brick-making machine that was truly portable and operated on-site. Just nine months after Jochen started his company, he was joined by business partner, Robert Plattner. Together, they created the M1 machine, which was used to create the very first home built with Hydraform blocks, in Witbank.
​
The unique interlocking, mortarless design means significant reductions in building costs, and is backed by Agrement Certificate 96/237 that is issued by the CSIR in Pretoria.
​
Today, Hydraform have developed a range of machines that offer a full turnkey functionality. From their flagship block-making machines, to equipment that produces various types of pavers, rooftiles, soil-sifting rotary screen machines and are used in over 40 different countries all across Africa and the world, and are used to build homes, universities, schools, churches, museums and many other developments.
​
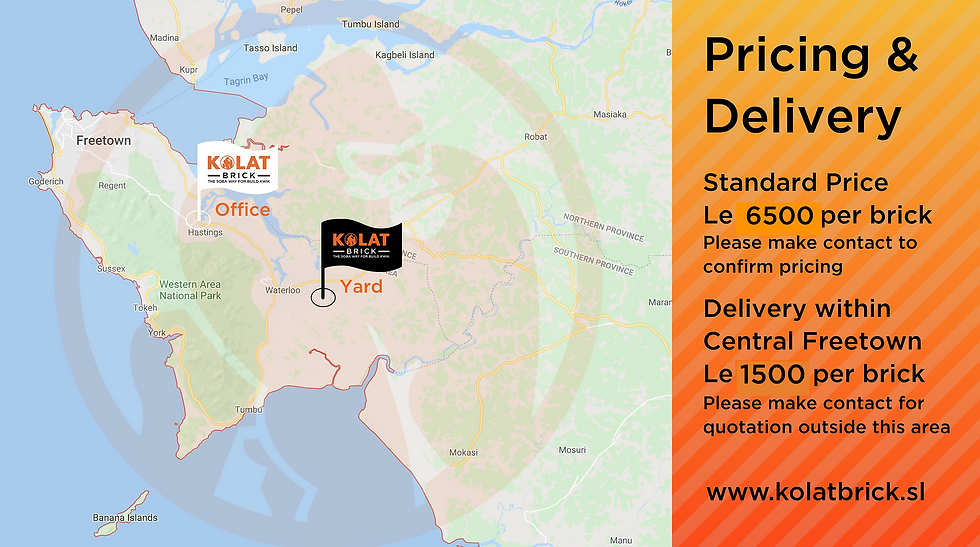